
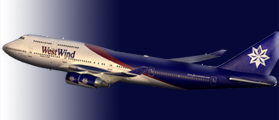
Advanced Pilot Programs - More about Turboprops and Propellers
Approved By
John Condon - Chief Pilot & Chief Administrative Officer
Last Updated: March 14th 2006
MORE ABOUT TURBOPROPS AND PROPELLERS
You have completed both the training and the check ride for WestWind's Beechcraft 1900 twin turboprop and Captain Ed Ward has now cleared you for line service. But, what do you really know about flying turboprops? What exactly is a 'turboprop?' These basic lessons will complement the Flight Operations Manual in discussing the critical parts of a turboprop and how they work together. We will also discuss techniques used on real world King Airs and how you may apply them in MSFS.
What is a turboprop? A turboprop is any airplane that uses a turbine (Jet) engine to provide power to a propeller. The propeller, not the jet, provides the bulk of thrust in a turboprop. The turboprop enjoys the reliability and performance of a jet engine and the economics of a propeller. So simply a turboprop is a prop powered by a jet engine.
You are being pulled through the sky by a propeller. The propeller on the B1900 is referred to as a constant speed, reversible, fully featherable all aluminum four bladed propeller. What a mouth full. We will start with the simplest terms. Four bladed simply means that the propeller has four blades. A four bladed propeller allows the pilot to create the same thrust as a three bladed propeller at lower RPMs. Thus the propeller is quieter. A quiet propeller is a good thing, both for the passengers on board and the noise sensitive communities surrounding many of the small airfields that the B1900 captain will find himself flying into. Why not then use a six bladed composite like on the DSH8Q series? Or at least a blade that is shaped more aerodynamically like the blades on the EMB120? Simply stated this is a cost concern of the manufacture, Beech. To bolt on a new propeller, means many months of flight-testing to earn an airworthiness release from the FAA. This would drive up the cost of the B1900, which has a selling point of being economical.
Beech choose to use aluminum blades due to how close the blades of the King Air are to the ground and the relatively simple maintenance required should blades become nicked or damaged. Composite blades are more durable, but when damaged almost always requires replacement. Aluminum blades can have nicks filed out returning it to service quickly.
Reversible means that the pilot can put negative, or reverse, pitch into the blades. There are three stages of reverse operation on the B1900 propeller; beta, ground fine, and reverse. Ground fine is used on the ground to slow the aircraft, usually during taxing operations while maintaining propeller rpm above 1,000 RPM. At propeller settings below 1,000 RPM Beech discovered that the propeller blades were creating a condition called prop oscillation damaging the hub and gear box. Thus Beech designed the prop to operate in the ground fine condition by setting the propeller into a beta setting and adding power to maintain RPM above 1,000. To further slow down the aircraft the pilot pulls the levers to the full ground fine position creating a low pitch + power setting. By lifting the power levers over the second gate the propellers are once again in a beta setting, creating zero thrust vector. Continuing to pull to the end of the reverse position the propellers move to a negative pitch and power is added changing the thrust vector to the front of the aircraft. MSFS does not replicate the ground fine setting, thus by selective use of reverse we can simulate ground fine and reverse. By just using a small bit of reverse simulates the slow down effect of ground fine and by using all of the reverse simulates lifting over the second gate into reverse.
Fully featherable means that the propeller, through the use of the propeller levers can be moved to a zero drag configuration. The individual propeller blades are attached to a propeller hub that contains a piston that is filled with oil to add pressure and drive the propellers to a flattened position determined by the low pitch stops. This position is known as the high RPM / low pitch position and when the engine is providing enough power represents 1700 RPMs. When the propeller levers are brought to the feather position, the oil is dumped from the hub and through counter-wound feathering springs and centrifugal weights the propeller blades are driven to the low RPM / high pitch position.This position is about 89° to the relative wind. The difference in a fully featherable propeller and a featherable propeller is in a normal aspirating engine if the propeller is allowed to coast down after an engine failure, anti-feathering pins will drop down limiting the propeller from reaching the full feathered position. These pins ensure that the propeller is maintained at a lower pitch for ease of starting the engine. The pilot of this type of airplane can ensure that the propeller goes to a fully feathered posistion by using the propeller control and selecting feather prior to the anti-feathering pins dropping down. In our fully featherable propeller even during an engine failure the propellers will still completely feather. Because we use a free turbine engine the propeller or N2 section of the engine is physically separated from the gas producer or N1 section allowing engine starts against the drag of a feathered propeller with relative ease. Just remember that fully featherable means the prop will feather regardless if we select feather on the propeller control or if the engine fails and the propellers coast down to the feathered position.
The final aspect of the B1900s prop is that it is a constant speed propeller. The first propeller used by the Wright Brothers and found on most single engine trainer airplanes is what is referred to as a fixed pitch propeller. Basically the designer takes a block of wood and carves out the propeller. This has the advantage of being inexpensive, but since the propeller is fixed it is set at one pitch setting not very efficient. The manufacture usually decides on a compromise in climb performance versus cruise performance. When the airplane increases pitch the propeller RPMs will tend to slow down and when the aircraft pitches down the propeller will tend to increase RPMs. The next evolution in the propeller was the variable pitch propeller. This propeller had a control in the cockpit that allowed the pilot to change the pitch of the propeller based on if the airplane was in a cruise or a climb configuration. This propeller had the advantage of multiple settings based on what type of performance the pilot required but still suffered from speeding up or slowing down during pitch or speed changes. Propeller manufactures then decided to put a governor on the propeller to control RPM. Thus the pilot would select a propeller RPM for the condition of flight that he was in, and through oil pressure, centrifugal forces, feather springs and speeder springs, the governor would maintain selected RPM.
The B1900 is a constant speed propeller controlled through three governors. The primary governor controls RPM from 1450 to 1700 RPM. The second governor, the overspeed governor limits the propeller to 1802 RPM. The final governor, which affects the propeller through engine output, is the fuel-topping governor limiting maximum rpm to 105% of selected RPM. Thus for takeoff the pilot selects maximum (1700 RPM) and through the primary governor the propeller will maintain 1700 RPM. However as soon as the pilot selects 1700 RPM the propeller does not immediately spin up to 1700 RPM. This is due to the engine not producing enough output to spin the propeller to 1700 RPM and the propeller is sitting on the primary low pitch stops. The low pitch stops are a dynamic control, which prevents the blades from completely flattening out in an attempt to reach selected RPM. As the pilot starts adding power propeller RPM increase until about 40% Q when the propellers 'are on the governors' and will maintain 1700 RPM. (40% is about the setting with zero airspeed on a standard day, density altitude and the speed in which the propeller is moving through the air all effect how fast the prop speed for a given %Q. Thus why sitting still it takes about 40% and while coming in for a landing the propeller starts coming off the governor at around 15 - 20% Q.
This is one area in which MSFS has completely ignored. Set the propellers to 1700 RPM and pull the power to the idle detent and the propellers create a tremendous amount of drag. I have personally flown a King Air at 220 Knot final to about two miles to touch down pulling all power off at that point and smoothly touching down at 111 Knots Vref. This drag is referred to as dynamic prop drag. Flying an approach in a B1900 is all about drag management. For MSFS you will have to use jet techniques and ensure that you are crossing your gates at correct speeds (power management) for approach and touchdown. I also recommend resetting the condition levers from high to low. In the actual aircraft the condition levers are left at high idle; to keep the RPM above 1,000 to prevent prop hub damage, keep engine above minimum air conditioning operation setting, and to minimize turbine lag when transitioning from landing to reverse. None of the above affects aircraft under MSFS. As soon as you decelerate below 202 you can drop the flaps to approach and that will assist you with deceleration to below your landing gear speed of 184. Upon reaching 184 deploy your gear to slow you to Vref+20, 141, for initial approach. Crossing the marker you should plan your deceleration to Vref, 121. Then use power to maintain Vref+5 to Vref-0, 126-121 during final approach. Unless landing to a short field I do not recommend full flaps. If you must land to a short field deploy full flaps early and use a Vref speed of 111.
Crossing the numbers you should be about 35’ above the runway, close the power levers and hold the airplane in a level attitude allowing it to settle toward the runway. For touchdown you will want to add just enough backpressure to allow the mains to touch the runway prior to the nose then gently lowering to nose onto the runway. As soon as the nose touches down pull the power into ground fine to initially slow down the aircraft, then if required into reverse. When performed correctly the airplane will gently touchdown with a distinct bark from first the outer mains then inner mains on the touchdown marker.
Now test yourself with a short quiz.
Answers:
1-B
2-C
3-A
4-C
5-B
6-A
7-B
8-C
9-B
10-A
Take care,
John Condon
Chief Administration Officer
Chief Pilot,
Head Of Training
NOT TO BE USED IN REAL WORLD FLIGHT. NO PARTS OF THIS ARTICLE MAY BE REPRINTED WITHOUT THE WRITTEN PERMISSION OF THE AUTHOR.